Verfahren zur Produktionsplanung und Produktionssteuerung in industriellen Unternehmungen
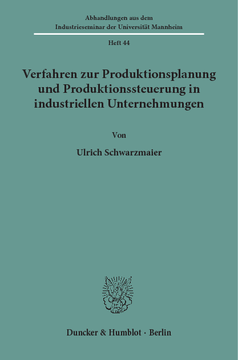
BOOK
Cite BOOK
Style
Format
Verfahren zur Produktionsplanung und Produktionssteuerung in industriellen Unternehmungen
Abhandlungen aus dem Industrieseminar der Universität Mannheim, Vol. 44
(1995)
Additional Information
Book Details
Pricing
Table of Contents
Section Title | Page | Action | Price |
---|---|---|---|
Vorwort | 7 | ||
Inhaltsverzeichnis | 9 | ||
Abbildungsverzeichnis | 17 | ||
Α. Einleitung | 19 | ||
I. Problemstellung | 19 | ||
II. Gang der Untersuchung | 25 | ||
B. Die Entwicklungslinien der Produktionsplanung und Produktionssteuerung | 28 | ||
I. Begriffe zur Produkionsplanung und -steuerung und ihre Entwicklung von der Arbeitsvorbereitung zum PPS-System | 28 | ||
1. Die Arbeitsvorbereitung: Rahmen fur die Planung und Steuerung im Produktionsbereich | 29 | ||
a) Der Begriff der Arbeitsvorbereitung | 29 | ||
b) Einordnung und Unterteilungsmöglichkeiten der Arbeitsvorbereitung | 34 | ||
2. Die Produktionsplanung und -steuerung | 36 | ||
a) Die Produktionsplanung | 37 | ||
aa) Die Planung | 37 | ||
bb) Die Einbindung der Produktion in das Planungswesen | 40 | ||
b) Die Produktionssteuerung | 45 | ||
3. Das PPS-System: Mittel zur Erfüllung der Funktionen "Produktionsplanung" und "Produktionssteuerung" | 49 | ||
a) Die Produktionsplanung und -steuerung im PPS-System | 49 | ||
b) Der Systemgedanke im PPS-System | 51 | ||
II. Geschichte und Entwicklungsstufen der Produktionsplanung und -steuerung | 54 | ||
1. Die Entwicklung der Arbeitsvorbereitung | 54 | ||
a) Die auf Erfahrungen beruhende Arbeitsvorbereitung | 56 | ||
b) Die technisch-wissenschaftliche Arbeitsvorbereitung | 60 | ||
c) Die betriebswirtschaftlich-wissenschaftliche Arbeitsvorbereitung | 66 | ||
2. Die Weiterentwicklung der Arbeitsvorbereitung bis zur Einfuhrung EDV-gestützter PPS-Systeme | 71 | ||
3. Unterschiede und Gemeinsamkeiten zwischen PPS-Systemen und der traditionellen Arbeitsvorbereitung | 79 | ||
C. Ziele und Funktionen der Produktionsplanung und -steuerung | 86 | ||
I. Ziele der Produktionsplanung und Produktionssteuerung | 86 | ||
1. Produktionswirtschaftliche Ziele als Grundlage zur Ableitung von Produktionsplanungs- und Produktionssteuerungszielen | 87 | ||
a) Begriff und Dimension des Zielelements | 87 | ||
b) Aufbau eines Zielsystems zur Ableitung von produktionswirtschaftlichen Zielen | 89 | ||
aa) Zielbeziehungen in einem Zielsystem | 90 | ||
(1) Die horizontale Ebene | 90 | ||
(2) Die vertikalen Beziehungen zwischen den Zielebenen | 91 | ||
bb) Die produktionswirtschaftlichen Ziele und ihre Beziehungen | 91 | ||
2. Die Ziele der Produktionsplanung und -steuerung | 95 | ||
a) Relevante Einzelziele | 95 | ||
aa) Formalziele der Produktionsplanung und -steuerung | 96 | ||
bb) Konkrete Sachziele der Produktionsplanung und -steuerung | 100 | ||
b) Zielbeziehungen zwischen den Zielen der Produktionsplanung und -steuerung | 109 | ||
aa) Komplementäre Beziehungen zwischen Formal- und Sachzielen | 110 | ||
bb) Konkurrierende Beziehungen zwischen den Sachzielen der Produktionsplanung und -steuerung | 112 | ||
c) Verschiebung der Zielgewichtung im Zeitablauf | 116 | ||
3. Anforderungen an die Wirksamkeit des eingesetzten Verfahrens zur Planung und Steuerung der Produktion | 119 | ||
II. Notwendige Funktionen zur Erfüllung der Sach- und Formalziele | 125 | ||
1. Simultane Verfahren der Produktionsplanung und -steuerung | 126 | ||
2. Sukzessive Verfahren der Produktionsplanung und -steuerung (herkömmliche PPS-Systeme) | 128 | ||
a) Gliederung nach der Fristigkeit | 129 | ||
b) Gliederung nach Funktionen | 131 | ||
aa) Die Datenverwaltung | 134 | ||
bb) Die Produktionsplanungsfunktionen | 136 | ||
(1) Die Produktionsprogrammplanung | 137 | ||
(2) Die Mengenplanung | 139 | ||
(3) Die Termin- und Kapazitätsplanung | 144 | ||
cc) Die Produktionssteuerungsfunktionen | 150 | ||
(1) Die Auftragsveranlassung | 151 | ||
(2) Die Auftragsüberwachung | 154 | ||
III. Erfüllung wichtiger Anforderungen und Ziele durch die herkömmlichen PPS-Systeme | 155 | ||
1. Schwächen der herkömmlichen PPS-Systeme in bezug auf die Zielerfüllung | 155 | ||
a) Schwächen durch den sukzessiven Aufbau der Verfahren | 156 | ||
b) Schwächen durch die Abgeschlossenheit der Systeme | 158 | ||
aa) Die Abstimmung mit der Konstruktion | 158 | ||
bb) Die Abstimmung mit der Arbeitsplanung und der Kostenrechnung | 159 | ||
cc) Die Abstimmung mit der Qualitätssicherung | 163 | ||
dd) Die Abstimmung mit dem Vertrieb | 164 | ||
ee) Die Abstimmung mit sonstigen Bereichen des Unternehmens | 165 | ||
c) Schwächen durch die einseitige Ausrichtung auf die Sachziele | 166 | ||
d) Schwächen durch den Einsatz von Heuristiken und standardisierten Durchlauf-und Vorlaufzeiten | 168 | ||
e) Schwächen durch fehlende Steuerungsmechanismen | 172 | ||
2. Die Erfüllung wichtiger Anforderungen durch ein PPS-System | 174 | ||
a) Die Flexibilität der eingesetzten Systeme | 174 | ||
aa) Die mangelnde Abstimmung auf die Gegebenheiten des Betriebstyps | 174 | ||
bb) Die mangelnde Einbeziehung von Umweltveränderungen | 176 | ||
cc) Mangelnde Flexibilität bei Eilaufträgen | 176 | ||
dd) Mangelnde Flexibilität bei Störungen | 177 | ||
b) Die Motivation der Belegschaft | 177 | ||
c) Überprüfung der Wirtschaftlichkeit und Übersichtlichkeit | 179 | ||
D. Kritischer Vergleich der neueren Konzepte der Produktionsplanung und -steuerung mit herkömmlichen PPS-Systemen | 181 | ||
I. Die Neuheit eines Verfahrens | 181 | ||
II. Einteilung der neueren Verfahren | 185 | ||
1. Einteilungen im Schrifttum | 185 | ||
2. Die Einteilung der neueren Verfahren in der vorliegenden Untersuchung | 187 | ||
III. Die ganzheitlichen Ansätze zur Verbesserung der herkömmlichen PPS-Systeme | 191 | ||
1. Verfahren nach dem Bring-Prinzip | 191 | ||
a) Das MRP II-Konzept | 193 | ||
aa) Grundlagen des MRP II-Konzeptes | 194 | ||
(1) Die Ebenen von MRP II | 198 | ||
(2) Die Abstimmung der Ebenen | 200 | ||
bb) Kritik am MRP II-Verfahren | 205 | ||
cc) Die grundlegenden Neuerungen von MRP II aus konzeptioneller Sicht | 211 | ||
b) Konzepte zur hierarchischen Produktionsplanung | 212 | ||
aa) Grundmuster der Modelle | 213 | ||
bb) Kritik und Neuheitsgrad | 215 | ||
c) Das OPT-Verfahren | 218 | ||
aa) Entstehung und Ziele | 218 | ||
bb) Die Grundregeln | 220 | ||
cc) Der Planungsablauf | 225 | ||
(1) Unregelmäßig, in größeren Abständen durchzuführende Tätigkeiten | 225 | ||
(2) Die regelmäßige Planung und Steuerung | 230 | ||
dd) Kritik am OPT-Verfahren | 235 | ||
(1) Die Zielerfüllung | 235 | ||
(2) Beurteilung hinsichtlich des Planungsumfangs und der Verwendung standardisierter Daten | 238 | ||
(3) Die Erfüllung der Anforderungen an OPT | 239 | ||
ee) Die grundlegenden Neuerungen von OPT aus konzeptioneller Sicht | 242 | ||
d) Die engpaßorientierte Disposition | 250 | ||
aa) Der Ablauf der engpaßorientierten Disposition | 251 | ||
(1) Die engpaßorientierte Materialdisposition | 252 | ||
(2) Die engpaßorientierte Kapazitätsdisposition | 256 | ||
bb) Kritik an der engpaßorientierten Disposition | 258 | ||
cc) Die grundlegenden Neuerungen der engpaßorientierten Disposition aus konzeptioneller Sicht | 262 | ||
2. Auf dem Hol-Prinzip aufbauende Verfahren | 267 | ||
a) Die Just-in-time-Politik | 268 | ||
aa) Der Just-in-time-Begriff | 268 | ||
bb) Ziele der Just-in-time-Politik | 274 | ||
cc) Die Idee und Weiterentwicklung der Just-in-time-Politik | 276 | ||
dd) Die schlanke Produktion als die dem Just-in-time übergeordnete Ebene | 286 | ||
(1) Die Produktentwicklung | 288 | ||
(2) Der Beschaflungsbereich | 290 | ||
(3) Die Produktion | 292 | ||
(4) Der Verwaltungs- und Vertriebsbereich | 297 | ||
ee) Geographische, soziale und kulturelle Besonderheiten in Japan | 298 | ||
ff) Kritik an der schlanken Produktion | 302 | ||
gg) Die grundlegenden Neuerungen der schlanken Produktion aus konzeptioneller Sicht | 308 | ||
b) Die Umsetzung der Just-in-time-Politik auf innerbetriebliche Bereiche mittels neuerer Verfahren zur Produktionsplanung und Produktionssteuerung | 310 | ||
aa) Das Hol-Prinzip | 310 | ||
bb) Das KANBAN-Verfahren | 315 | ||
(1) Die KANBAN-Idee und die Ziele bei Einsatz des KANBAN-Verfahrens | 316 | ||
(2) Grundlagen des KANBAN-Verfahrens | 318 | ||
(a) Das Regelkreissystem zur dezentralen Steuerung | 320 | ||
(b) Die KANBAN-Karte als Informationsträger und Optimierungsgröße | 324 | ||
(c) Die Größe und Anzahl der Behälter | 326 | ||
(3) Die Elektronische Datenverarbeitung in KANBAN-Systemen | 328 | ||
(4) Voraussetzungen für den KANBAN-Einsatz | 330 | ||
(5) Anwendungsbereiche des KANBAN-Systems | 334 | ||
(6) Kritik am KANBAN-Verfahren | 339 | ||
(a) Beurteilung hinsichtlich der Ziele | 340 | ||
(aa) Die Formalziele | 340 | ||
(bb) Die Sachziele | 345 | ||
(b) Das "Durchlaufzeit-Syndom" im KANBAN-Verfahren | 351 | ||
(c) Beurteilung hinsichtlich der Komplexität und Flexibilität | 353 | ||
(d) Beurteilung hinsichtlich der Motivation und der Qualifikation des Personals | 354 | ||
(e) Abschließende Beurteilung hinsichtlich der Rationalisierungseffekte | 356 | ||
(7) Die grundlegenden Neuerungen von KANBAN aus konzeptioneller Sicht | 357 | ||
cc) Das Fortschrittszahlenkonzept | 367 | ||
(1) Idee und Ziele des Fortschrittszahlenkonzepts | 368 | ||
(2) Grundlagen des Fortschrittszahlenkonzepts | 370 | ||
(a) Die Festlegung der Kontrollblöcke | 370 | ||
(b) Arten und Funktionen der Fortschrittszahlen | 372 | ||
(c) Wiederkehrende Planungsaufgaben | 377 | ||
(d) Die Steuerung der Produktion | 379 | ||
(3) Das Hol-Prinzip im Fortschrittszahlenkonzept | 381 | ||
(4) Die Steuerung von Fertigungslinien bei Einsatz des Fortschrittszahlenkonzepts | 383 | ||
(5) Kritik am Fortschrittszahlenkonzept | 383 | ||
(a) Die Sach- und Formalzielerfüllung | 384 | ||
(b) Die mitarbeiterbezogenen Effekte | 387 | ||
(c) Bewertung hinsichtlich der Flexibilität der Produktion | 388 | ||
(d) Bewertung hinsichtlich der Komplexität des Konzepts | 389 | ||
(e) Bewertung hinsichtlich der praktischen Einsatzmöglichkeiten | 390 | ||
(f) Der Abstimmungsgedanke | 391 | ||
(6) Die grundlegenden Neuerungen des Fortschrittszahlenkonzepts aus konzeptioneller Sicht | 392 | ||
c) Die Umsetzung der Just-in-time-Politik auf überbetriebliche Problemkreise | 395 | ||
aa) Charakteristika von überbetrieblichen Just-in-time-Lieferbeziehungen | 396 | ||
(1) Die Rahmenverträge | 396 | ||
(2) Auswahl der Lieferanten | 403 | ||
(3) Die Organisation des Transports | 405 | ||
(4) Die Organisation des Abrufs | 407 | ||
(5) Der Einsatz von Just-in-time-Lägern | 410 | ||
bb) Einsatzmöglichkeiten der neueren Verfahren zur innerbetrieblichen Produktionsplanung und -steuerung fur überbetriebliche Fragestellungen | 413 | ||
(1) KANBAN auf überbetrieblicher Ebene | 413 | ||
(2) Das Fortschrittszahlenkonzept auf überbetrieblicher Ebene | 415 | ||
cc) Erfolgsfaktoren und Probleme von Just-in-time auf überbetrieblicher Ebene | 416 | ||
IV. Ansätze zur Verbesserung von Teilfunktionen der herkömmlichen PPS-Systeme | 420 | ||
1. Die belastungsorientierte Auftragsfreigabe | 421 | ||
a) Entwicklung, Idee und Zielschwerpunkte des Verfahrens | 421 | ||
b) Darstellung der belastungsorientierten Auftragsfreigabe | 423 | ||
aa) Zusammenhänge zwischen Leistung, Bestand und Durchlaufzeit | 424 | ||
bb) Der Verfahrensaufbau | 429 | ||
(1) Die Termin- und Belastungsschranke | 430 | ||
(2) Die statische Betrachtung der Auftragsfreigabe | 432 | ||
(3) Schritte des Verfahrens in einer Periode | 435 | ||
(a) Die Terminierung | 436 | ||
(b) Die Abwertung | 437 | ||
(c) Die Belastungsprüfung und die Auftragsfreigabe | 438 | ||
c) Kritik an der belastungsorientierten Auftragsfreigabe | 439 | ||
aa) Die Bewertung hinsichtlich der Zielerfullung | 439 | ||
bb) Die Wahl der Schranken, die Abwertungsproblematik und die Problematik des Durchlaufzeitsyndroms | 444 | ||
cc) Die Integration der belastungsorientierten Auftragsfreigabe in ein herkömmliches PPS-System | 447 | ||
dd) Die Bewertung hinsichtlich der Flexibilität bei Eilaufträgen und der Flexibilität des Einsatzspektrums | 448 | ||
ee) Die Bewertung hinsichtlich der Anforderungen an ein PPS-System | 450 | ||
d) Die grundlegenden Neuerungen der belastungsorientierten Auftragsfreigabe aus konzeptioneller Sicht | 453 | ||
2. Die retrograde Terminierung | 457 | ||
a) Ansatzpunkt des Verfahrens | 458 | ||
b) Der Verfahrensaufbau | 459 | ||
c) Kritik an der retrograden Terminierung | 462 | ||
d) Die grundlegenden Neuerungen der retrograden Terminierung aus konzeptioneller Sicht | 466 | ||
3. Die Input- / Output-Control | 470 | ||
a) Ansatzpunkte des Verfahrens | 470 | ||
b) Der Verfahrensaufbau | 471 | ||
c) Die Erweiterung des Verfahrens zu einem kostenorientierten Input- / Output-Control nach Missbauer und Zäpfel | 472 | ||
aa) Die kostenorientierte Input- / Output-Control bei von der Mengenplanung unabhängiger Kapazitätsbelegung | 473 | ||
bb) Die kostenorientierte Input- / Output-Control bei gemeinsamer Mengenplanung und Kapazitätsbelegung | 475 | ||
d) Kritik und Neuheit des Input- / Output-Control | 477 | ||
aa) Kritik und Neuheit des einfachen Input- / Output-Control | 478 | ||
bb) Kritik und Neuheit des kostenorientierten Input- / Output-Control | 479 | ||
4. Die bestandsgeregelte Durchflußsteuerung | 483 | ||
a) Anstoß und verfolgte Ziele | 483 | ||
b) Der Verfahrensaufbau | 485 | ||
c) Kritik an der bestandsgeregelten Durchflußsteuerung | 487 | ||
d) Die Neuheit der bestandsgeregelten Durchflußsteuerung | 490 | ||
5. Die kapazitätsorientierte Materialwirtschaft | 491 | ||
a) Anknüpfungspunkte der kapazitätsorientierten Materialwirtschaft | 491 | ||
b) Der Verfahrensaufbau der kapazitätsorientierten Materialwirtschaft | 493 | ||
c) Kritik an der kapazitätsorientierten Materialwirtschaft | 495 | ||
d) Die Neuheit der kapazitätsorientierten Matrialwirtschaft | 497 | ||
6. Die Planung mit verdichteten Daten | 497 | ||
a) Grundlagen | 498 | ||
b) Kritik und Neuheitsgrad | 499 | ||
7. Die Expertensysteme | 501 | ||
a) Charakteristika der Expertensysteme | 501 | ||
b) Einsatzgebiete von Expertensystemen | 505 | ||
c) Expertensysteme in der Produktionsplanung und -steuerung | 506 | ||
aa) Das ISIS-Expertensystem und deren Weiterentwicklung | 508 | ||
bb) Das PEPS-Expertensystem | 511 | ||
cc) Das SOJA-Expertensystem | 512 | ||
d) Kritik an den Expertensystemen | 513 | ||
e) Die Neuheit der Expertensysteme | 517 | ||
V. Ergebnisse der Neuheitsprüfung der Verfahren zur Produktionsplanung und -steuerung | 518 | ||
E. Typologische Aspekte bei der Auswahl eines Verfahrens zur Produktionsplanung und Produktionssteuerung | 520 | ||
I. Der typologische Ansatz | 521 | ||
1. Die Bedeutung der typologischen Methode | 521 | ||
2. Grundlagen der typologischen Methode | 522 | ||
II. Einteilung von Industriebetrieben in Typen | 523 | ||
1. Die Organisationstypen der Fertigung | 525 | ||
2. Die Leistungswiederholungstypen | 528 | ||
III. Anforderungen der Typen an die Produktionsplanung und -steuerung | 531 | ||
1. Anforderungen der Organisationstypen der Fertigung an die Produktionsplanung und -steuerung | 532 | ||
a) Anforderungen bei einer Werkstattfertigung | 532 | ||
b) Anforderungen bei einer Fließfertigung | 534 | ||
c) Anforderungen bei einer Baustellenfertigung | 536 | ||
2. Anforderungen der Leistungswiederholungstypen an die Produktionsplanung und -steuerung | 537 | ||
a) Anforderungen bei einer Einmalfertigung | 538 | ||
b) Anforderungen bei einer Einzel- und Kleinserienfertigung | 540 | ||
c) Anforderungen bei einer Großserienfertigung | 541 | ||
d) Anforderungen bei einer Massenfertigung | 542 | ||
IV. Bildung von Verbundtypen | 544 | ||
V. Die Eignung der Verfahren zur Produktionsplanung und -steuerung für bestimmte Industriebetriebstypen | 545 | ||
1. Die Eignung der Gesamtansätze nach dem Bring-Prinzip fur bestimmte Industriebetriebstypen | 546 | ||
a) Die Eignung des herkömmlichen MRP-Systems, des MRP II-Systems und der hierarchischen Produktionsplanung | 546 | ||
b) Die Eignung von OPT | 549 | ||
c) Die Eignung der engpaßorientierten Disposition | 551 | ||
2. Die Eignung der Verfahren nach dem Hol-Prinzip für bestimmte Industriebetriebstypen | 553 | ||
a) Die Eignung des KANBAN-Verfahrens | 553 | ||
b) Die Eignung des Fortschrittszahlenkonzepts | 555 | ||
3. Die Eignung der Teilansätze fur bestimmte Industriebetriebstypen | 557 | ||
a) Die Eignung der belastungsorientierten Auftragsfreigabe | 558 | ||
b) Die Eignung der bestandsgeregelten Durchflußsteuerung | 560 | ||
c) Die Eignung der retrograden Terminierung | 561 | ||
d) Die Eignung der Expertensysteme | 561 | ||
e) Die Eignung der sonstigen Verfahren | 562 | ||
4. Die Eignung der Verfahren zur Produktionsplanung und -steuerung im Überblick | 564 | ||
F. Schlußbemerkung | 567 | ||
Literaturverzeichnis | 569 |